
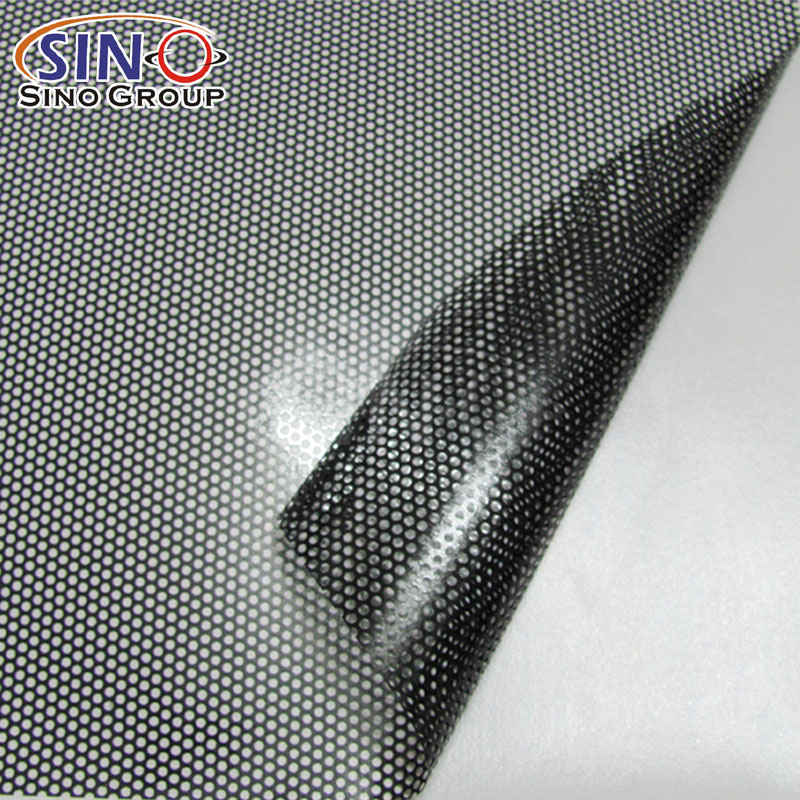
The Arizona printer, printed at dpi of 309 used a six colour process. One of the first successful solvent printers was the Arizona 180. Early solvent printers were unreliable and took a vasty amount of daily / weekly maintenance to keep them running. Untreated substrates make solvent printing much more durable than standard aqueous water-based inks. The solvents soften the material, and this allows the pigments to attach to the substrate. The inks can be printed onto uncoated vinyl and other roll media. More passes increase the time taken to print. This pass rate can be adjusted up to 24 passes which increases quality and resolution dramatically. More commonly prints are produced on either a 6 or 8 passes. Modern-day solvent printers can print on several quality settings which are known as passes. Print qualityīanding is a term for lines in the print which are more noticeable when printing bi-directionally because of the ink firing onto the substrate from a different direction on each pass of the head. Uni-directional settings are better for print projects that require high grade, fine-detailing. The print head will drop ink, for example, left to right and then upon its return, moving right to the left the media will be advanced, and the process will start over. The print head only moves one way when printing. Uni-directional printing is more accurate as the drop position doesn’t have to match in the same way. The speed the print head movement also have an impact on drop position calculations. The predictions made ensure that the ink drops fall to the same position when travelling from either direction. What does the term ‘drop position’ mean?ĭrop positions calculations need to made for the movement in both directions. Drop position refers to a calculation of where the ink will drop onto the print surface from the time it fires from the head. Drop position can be adjusted to make the quality sharper. Bi-direction printing is faster but slightly more inferior quality-wise than uni-directional printing due to the ink on each pass is firing from the opposing direction. Once a pass of the head as moved from left to right, the media will advance one pass and then the process will repeat this time travelling from right to left. What is a Bi-Directional Print process?īi-directional printing will spray ink on the material travelling left to right. The ink hits the surface in the same place each pass reducing banding. Uni-directional printing is slower but gives higher accuracy. Uni-directional means ink will only spray on the surface in one direction. Solvent printers can often also print unidirectionally. Print heads usually print bi-directionally meaning they spray ink when moving in both directions. The surface of the Piezo print head contains tiny, microscopic apertures. Print nozzles fire ink onto the print media. Most modern-day solvent printers print at around 800-1500dpi and have 100’s of print nozzles per head. Solvent printing is generally a higher resolution print method as apposed to UV printing. The ink hits the substrate with exceptional pinpoint accuracy. Piezo print heads charge electrically and fire ink at the printed substrate. Solvent prints are fully waterproof once dry. These Eco and Mild solvents have slower drying times due to the lack of acetone. Mild solvents generally use Glycol or Glycol Ether. Manufactured from petroleum-based the inks contain substances such as acetone: mild solvents and eco solvents which are less harsh. The term solvent refers to ink that doesn’t contain water. Large format and wide format printers have been using solvent printing technology since the mid to late 1990s.
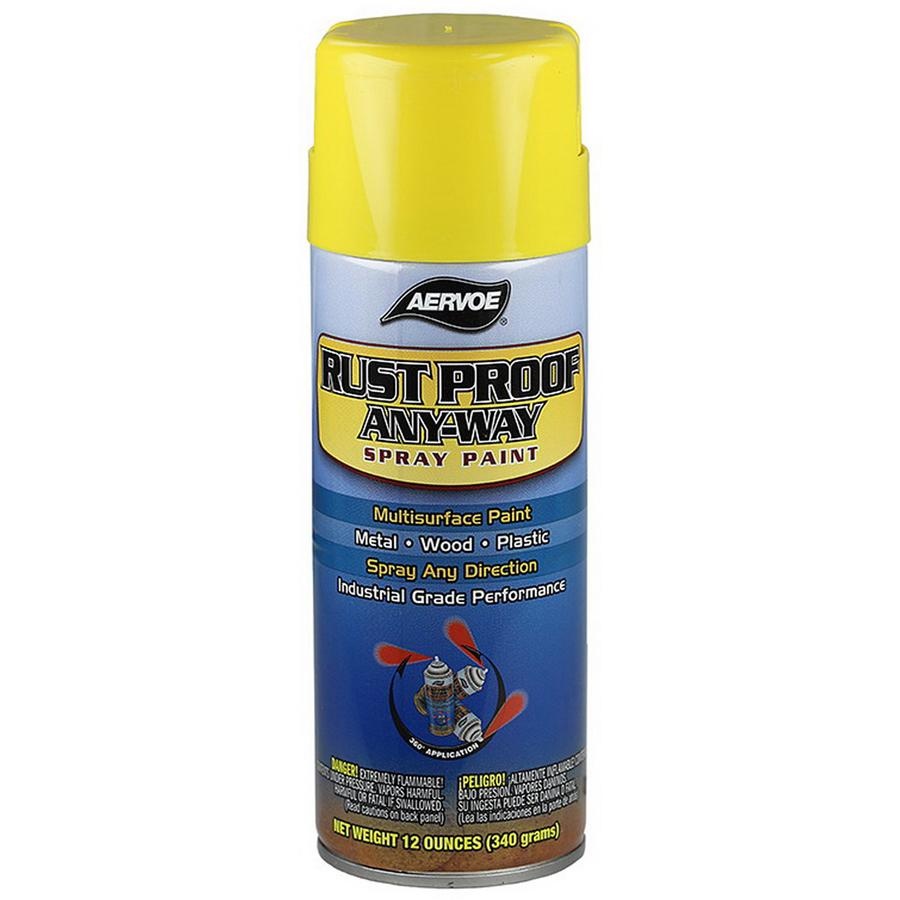
